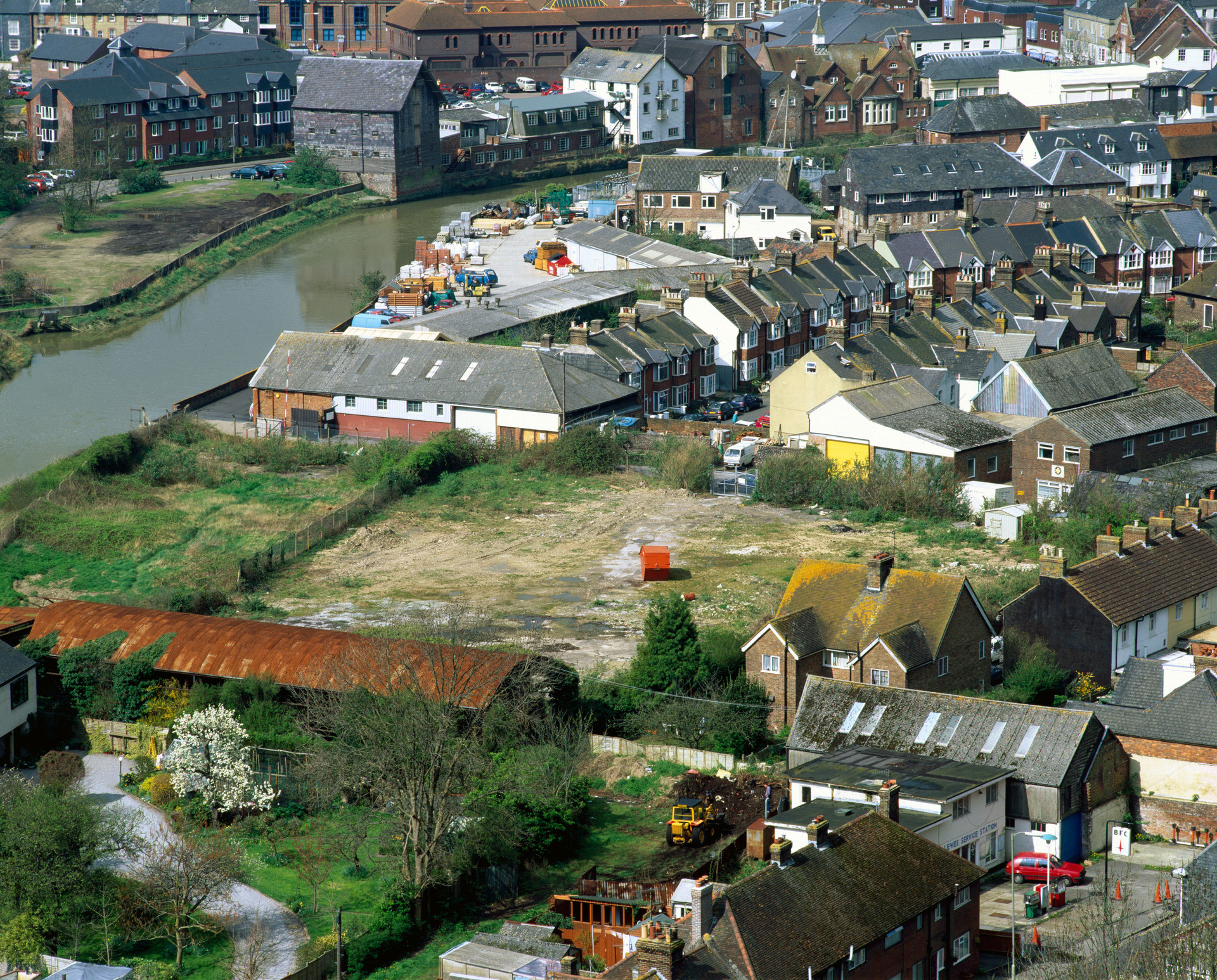
With the use of brownfield sites rising following pressure from Government and various environmental lobbies, unseen threats in construction foundations are occurring more frequently. However, through specifying the correct waterproofing systems these invisible dangers can be countered.
Brownfield sites often encounter issues such as existing footings, live services, or even Central London’s Tube network. Plus there are effects of contamination, particularly on old industrial sites or places like former petrol stations, which need to be considered. For example, where hydrocarbons and chemicals have entered the subsoil, or organic matter is breaking down, steps must be taken to guard against carbon dioxide or methane migrating into the structure.
Urban regeneration projects and other redevelopment situations must now adhere to the recommendations of the recently revised BS8485:2015 and the NHBC ‘Traffic Light’ scheme. Which, places emphasis on “justification” for the precautions selected as well as record keeping in relation to risk assessment and design decisions. Therefore, with methane alone classed as being explosive & asphyxiant - making the need to exclude such gases essential - we always advise engaging with us from an early stage.
The BS8485:2015 code of practice looks specifically at limiting the ingress of methane and carbon dioxide ground gases, both attributed to brownfield sites. Designating each site as having a Characteristic Situation score of 1-6. This is calculated through looking at the concentration and flow rates of hazardous gases present on site. A Characteristic Situation 1 is the only site environment, which doesn’t require any specific gas protection methods.
Once the Characteristic Situation is calculated, it’s necessary to understand the ‘Type’ of building proposed as defined in BS8584:2015. There are 4 different ‘Types’ of building: Type A – D. A private single dwelling such as a house would be considered a Type A building, for example, whereas a large open warehouse might be classified as a Type D building. Type A buildings offer greater potential to exposure for its inhabitants than a Type D building, meaning that more gas protection is required in a Type A building than a Type D.
Once this is understood – a suitable set of gas protection methods can be considered for the three different areas of the structure, each of which can be influenced to provide gas protection. These are the structure itself, ventilation beneath the structure and the provision of a continuous gas resistant membrane.
Much like with other waterproofing specifications, a decision must be made as to whether the membrane should be positioned beneath the floor or above it. At this stage we look to provide guidance on the form of the sub-structure. Aiming to benefit not only the effectiveness or the waterproofing and gas protection, but also the overall cost and programme benefits to the installation sequence.
It’s important, for instance, to avoid the creation of pockets beneath a floor – such as between ground beams – where hazardous gases could collect. We also look to help contractors through making use of systems that are easy to apply and facilitate the most efficient construction sequence.
Our Gas Seal Black product responds to this challenge through being a four layer, low-density polyethylene gas barrier that can be installed above or below most types of floor construction. It also forms a highly effective DPM along with offering dependable, economic protection against hydrocarbons, methane, carbon dioxide and radon; as well as moisture from the ground.
The overlaps to Gas Seal Black can be seam welded and it’s available with a selection of ancillary products. Permitting effective installation across complex building footprints and enabling ground gases to be vented to the outside atmosphere via special ground boxes or bollard vents.
Where below ground tanking applications are concerned, Sheetseal GR or Structureseal CPT offer BS8485 accredited performance against gas ingress, as well as protecting against water ingress.
As heavy industry in the UK declines and resistance to erosion of the Green Belt is unlikely to lessen, contractors, consultants and their clients have an increasing need to work on brownfield sites. Making the need for specialist knowledge on how to design for integrated gas protection solutions more and more necessary.
For further information on RIW products and capabilities for brownfield sites call our technical team on 01753 944200.
By Alex Massingham, National Sales Manager at RIW Ltd.